A toast to manufacturing
on LinkedIn:
We are all manufacturers. Without appreciating it we manufacture products ourselves every day. Think back to breakfast this morning – did you make toast?
Most mornings my son has toast for breakfast. The process of making his toast mimics the work I do every day at CDP in the development and commercialisation of manufacturing processes for medical and drug delivery devices, and which my colleagues undertake for consumer products. At all levels – medical, commercial, domestic – the principles are the same, it’s the depth to which each stage is undertaken that differs and knowing how deep to go.
Creating breakfast starts by selecting the bread, the critical raw material of the toast making process. It’s important to have bread available – a rather simple stock management exercise that fails more often than I’m prepared to admit. The nicest bread comes from a local shop and this shop sits at the top of our approved suppliers list, although we often dual source from other local shops. An additional consideration is the type of bread (the raw material specification). White is preferred over brown, fresh preferred over sliced. This specification also helps to determine whether the bread is likely to go stale or mouldy before it’s used. Shelf life and storage conditions play a huge part in this, as they do for many consumable goods and drug combination products.
The manufacturing equipment we use for conversion of bread into toast is a toaster. An open grill or fire would do the job but are more prone to process variation resulting in a burnt or underdone offering. I consider these options to be more akin to manual, proof of concept processes and the more advanced, semi-automated toaster frees up the operator to do other tasks, like packing a school bag or making a cup of tea. Getting a new toaster is fraught with uncertainty! Once out of the box it’s plugged in to check that it works (installation qualification) and then a series of trials is embarked upon to find the right setting for a perfectly done slice of toast (operational qualification). It then remains on this setting for a while to prove that it works consistently several mornings in a row (performance qualification). The toaster is now “validated”, and everything is fine until the settings are changed because someone wants a teacake and you need to try and remember your previous settings (change control). Luckily, we can reduce the stress and uncertainty of new process equipment by thinking about and documenting these risks and challenges up front and developing specifications and designs that fulfil your needs – you’ll have had specifications for your toaster too, even if this was only an undocumented request that it matches the kettle.
After emerging from the toaster, the toast undergoes a visual inspection (quality control) to confirm that it’s suitable (within specification). If it’s burnt it becomes a reject and goes in the bin, if it’s underdone then rework is appropriate as it can go back in the toaster although more attention is required for this phase.
The final stage is toppings; usually butter and honey, and presentation. This is the area which has historically generated the most complaints and it mirrors the drug delivery market where most complaints are generated due to labelling and packaging errors.
As we sit eating our breakfast I can reflect on the current low level of complaints and how it’s taken us years to develop an effective morning routine. The same is true at CDP where years of experience enable me to help clients navigate through the development of complex manufacturing processes and their accompanying regulations.
My top tip for not getting burnt would be to talk to all the key stakeholders and understand the following;
- The final product – what needs to be produced and in what quantity; the difference between making toast for two and making toast in a busy café.
- The scope of the manufacturing process – it is just toast, or will you also need it for bagels, crumpets and teacakes?
- The expectations of the consumer/patient and the regulatory environment – do you need the toast to be gluten free? or made in a certifiably hygienic environment?
And remember, in the end we are all manufacturers – even if the scale and complexity of our products are worlds apart.
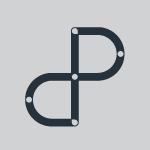
Caroline Zakrzewski
Consultant Drug Delivery Devices Scientist