Bridging a cultural gap in product innovation
on LinkedIn:
Industrial design (ID) and engineering skills are different, yet both are crucial to successful new product development (NPD). But as anyone involved will have experienced, tensions can arise due to the approaches and goals of different members of the team.
Having attended both art school to study ID and university to study mechanical engineering, I work between the two disciplines, from front end ‘user centred’ concept generation through to detailed design for manufacture. As such, I have experienced these tensions, engineers often pressing for performance and the industrial designers for the user experience they believe is so essential. The worst-case scenario is when everyone misses their goals. So how do we achieve the best outcome?
This is where speaking both design languages can provide benefits. Having empathy and taking the time to understand the underlying design aims from both sides allows for better integration of the end product.
It is important that the NPD team recognises this gap and actively works towards creating a culture where collaboration is the norm. Fortunately, there are some simple measures that can encourage a culture of information sharing and a free flow of ideas. We do this here at CDP and one example is our ‘Friday Innovation Forum’, a weekly event involving different themes and speakers sharing learnings across all disciplines. Another format is a jumbo size computer monitor in our central coffee area which displays new ideas to inform and educate, stimulating coffee time discussions around hot topics and helping to align thinking across disciplines.
With my design hat on, I have a natural appreciation of ID so I spend time trying to understand the artistic intent of what the industrial designer has created and what they are trying to achieve, you can then start working with them to create solutions that embody everyone’s requirements. For example, to start this process, I like to ask:
“What is the ‘hero shot’ you have in your mind for the product, if it was on a billboard or on the side of a building – what is it that you are trying to convey?” By asking that question I’m probing into what the industrial designer’s thought process is and creating a space where we can consider alternative solutions that could benefit all parties.
This is much easier if all the project disciplines are involved right from the start of the project. As an engineer I try to communicate the development journey, performance requirements and operating constraints across the whole team as they become known or change. By highlighting the difficulties as and when they occur it allows the ID team, or any other skill group for that matter to react and develop concepts in parallel that consider the new realities. This is best achieved through informal chats as the program progresses, it doesn’t always have to be in an official review meeting.
I favour elegant design solutions and try to stay away from what I call “glamour caps”, mouldings that have no other purpose than to hide an undesired feature. If the team all think in this way then you can create integrated designs with purpose as well as aesthetics.
It’s never a good idea to crowbar a new design into an already developed architecture. And similarly, it’s never easy to develop the usability and aesthetics of the product when too much is set in stone. By bridging the gap between these two disciplines and steering the development journey away from the ‘it’s your problem’ attitude you can create fantastic products that look good and have high performance.
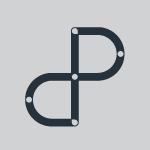
Lewis Ho
Consultant Design Engineer