Can lasers improve your manufacturing efficiency?
on LinkedIn:
In the last 20 years, evolution in laser technology has lowered cost, improved performance and reliability and made a wide range of laser types available and accessible for industrial applications.
Lasers produce an intense and coherent beam of light that can be focused to heat or vaporise a substrate. Different laser types produce different wavelengths and this is important to match this to the substrate. The power is also an important factor and depends on the material, process and speed. With a large number of lasers on the market, it can be a challenge to choose the right one for the job. So which one best fits your application? Let’s look at the two most common types.
Carbon dioxide (CO2) lasers are one of the most established and affordable options. Typically operating in the mid infrared wavelength band and with relatively high efficiency, they are most often used for cutting plastics and wood and drilling and marking other materials.
Nd:YAG (neodymium-doped yttrium aluminium garnet, no less!) are solid-state lasers typically operating in the near infrared wavelength band and are most often used for applications like cutting and welding of steel and other alloys. This type of laser can be easily forced to generate high energy and short duration pulses (using Q-switching), which can perform micromachining and micro drilling.
Lasers generating pulse durations in the pico and femtosecond ranges are best used for demanding cutting, structuring and drilling applications, which require minimal thermal distortion to the processing site surroundings. This is often referred as a ‘cold’ laser processing — where the laser high pulse energy and short duration converts the material directly into vapour phase. This results in negligible heat affected zone and sharp processing features. This outcome is particularly important in applications like drilling fuel injection nozzles and cutting cardiovascular stents, for which the short pulsed lasers are often used.
The laser technologies I’ve described are only a fraction of the range of laser variants and related applications available. Aside from application, wavelength, power, operation mode, size and overall cost are also factors to consider.
When developing a laser based manufacturing system after the laser itself, the beam delivery system is the next major factor to consider. There is the basic requirement to get the light to the workpiece with minimum losses, but also it often must be accurately steered and focused to follow the shape to be processed. Optical systems are susceptible to shock and vibration, so robust mechanical design is essential and especially important for applications where optics contamination may result in premature system failures, which lead to high running cost and frequent down times.
First steps
The laser interaction with the workpiece depends on many factors and it’s often difficult to exactly predict the outcome so it is important to try it! Each process is different and even a small thing, like changing an additive in a plastic part can have an big impact on the quality of the final result. We work with a number of partners who can undertake these tests quickly and at minimum cost. The knowledge gained at this early stage is essential to specify the new process or system.
Building a test rig
Once the specification is defined the next step is to build a ‘proof of concept’ test rig. This is an effective method to evaluate the laser and the system performance against the requirements specification. At this stage a Design of Experiments (DOE) method can be employed to determine the relationship between the key factors that affect the system output. The resulting information can be used to further refine the production system and inform the quality plan and process qualification strategy.
Moving towards production
Once the technology behind your laser application is proven then we can start to specify and build the production system itself. This will add materials handling, automated inspection and test and safety systems.
At CDP our physics team includes several experts in laser technology and our simulation experts can help specify new laser applications. Our manufacturing team have the expertise to design and build custom systems for both special purpose and high speed manufacturing applications. If you have any questions please get in touch at hello@cambridge-design.co.uk.
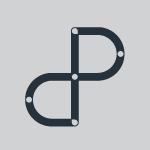
Dariusz Zak
Product Development Physicist