Cost and access are no longer barriers to high fidelity computer simulation in product design
on LinkedIn:
From coffee makers to asthma inhalers, oil wells to micro fluidic medical diagnostics, a thorough understanding of fluids is vital to optimise product performance. Fluid flow is complex and can provide significant challenges when it defines product performance. Simulation of fluid flow using computational fluid dynamics (CFD) provides critical insights into how complex systems will function, allowing designers to understand, predict and optimize behavior not possible by other means.
Today cloud-hosted applications and services are everywhere — from data storage, to web services and on-demand compute power, to name a few. On-demand compute power is a key enabler for performing more accurate and physically representative – high fidelity – numerical simulations.
CFD algorithms are demanding for compute power, in terms of flops, RAM and memory bandwidth. To generate accurate models of complex flows often requires clusters of hardware with fast optical interconnects. Before the Cloud, this required significant on-site hardware and not-insignificant associated overheads including administration, maintenance and thermal management.
Continued hardware performance development has reduced the footprint per unit of compute power, allowing cloud providers to house and maintain significant capacity. So what does this mean for the use of CFD in the design process?
Workstations have become more and more powerful and decent-sized models can now run under your desk. However for more demanding applications (where capturing the multi-scale behavior of turbulence is important), you are limited to Reynolds Averaged (RANS) turbulence modelling methods unless you have to access cluster level compute power. Despite the number of cores you can now get on Xeon chips, CFD algorithms quickly become memory bandwidth-limited once the cores per chip exceeds the memory channels per socket. GPUs are useful here, but a lot of the original algorithms developed for CFD codes have not been updated to take advantage of these architectures. The recent emergence of GPU-specific codes is an exciting development for CFD.
Access to cluster-level power in the Cloud allows large, complex CFD problems to be addressed using the more advanced turbulence models on-demand with no operational overhead, with the only time scale being the set-up, solution and post-processing of the model. High fidelity, scale resolving turbulence models, such as Detached Eddy Simulation (DES), can show fluid behavior and performance characteristics not seen with the Reynolds Averaged models.
Cloud usage options are considerable — from cloud simulation-specific vendors offering open source software and ‘bring your own license’ commercial packages, cloud solutions offered by the big commercial software companies themselves, to the whole cloud infrastructure package offerings from Amazon, Microsoft and Google.
There have always been concerns over cloud-based data security, motivated by the simple concern of not knowing where the hardware is or who may access it. Today, the major providers take care of the physical security of the data centre and the hardware — leaving customers to look after the security of the infrastructure they are using. As a result, lots of sensitive data is currently processed in the Cloud with genome sequencing, clinical trial data processing and financial data storage and management all being performed on Amazon’s web services (AWS).
Whether you use commercial or open source CFD software, the ability to include high fidelity CFD into your design process is incredibly valuable. It can be the difference between good and great product performance and offer greater insight into important flow structures and behavior. To maximise cost effectiveness, the use of open source software takes the license element out of the equation and allows maximum control over the numerical implementation. It also provides the opportunity to modify the algorithms as required. This is the approach we take at CDP for complex problems dominated by fluid flow, providing greater insight and maximising performance potential.
If you have any questions about using high fidelity Computational Fluid Dynamics for your product development please get in touch with me at hello@cambridge-design.co.uk.
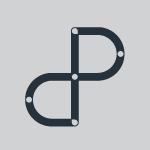
Dr Simon Hubbard
CDP's simulation specialist