Exploding some of the myths about product safety
on LinkedIn:
Hardly a week goes by without the press or social media picking up on a story, often accompanied by dramatic video, of batteries overheating and even in some cases ‘exploding’ in a consumer product – raising serious concerns about product safety among both consumers and manufacturers. In reality, these incidents are quite rare compared with the number of products sold. But when they occur they are very serious – both at a personal level for the user and at a reputational level for the manufacturer – with a lingering impact from product recalls and loss of brand value.
The vast majority of cases are entirely avoidable through robust product engineering and manufacturing approaches. Many incidents are, in fact, due to failures of the lithium-ion batteries used to power the device. This technology has a long history of issues in products as diverse as the Boeing 787 Dreamliner passenger aircraft, where battery pack fires were widely reported, and laptops and mobile phones – in particular, the Samsung Galaxy Note7 where Samsung had to recall millions of the handsets due to widely publicised handset fires and it led to a ban on taking the handsets on aircraft in the US. The problems that cause lithium cells to overheat and eventually catch fire or explode are well known – but we continue to see these failures occurring in devices on the market, due to either circuit design issues, incorrect mechanical embodiments or poor cell manufacturing processes. Some instances have even been blamed on ‘user error’. But we disagree on this point – in a properly designed product, user errors should not lead to hazards.
For example, in the case of e-cigarettes, especially those where the battery is interchangeable and charged outside the device, ‘user error’ is cited as a major contributor – with cells being charged with whatever charger is to hand, potentially driving them at too high a voltage or current, or cells even being replaced with low-quality, under-rated or damaged cells. Some of the most dangerous battery failures occur when the device fails in the owner’s trouser pocket – for example, when unprotected spare batteries are kept in a pocket along with loose change and keys, which then cause a direct short across the cells. These failures, and subsequent high-profile reporting of injuries, would have been avoided with good design practices and understanding of common usage behaviours. Product design engineers have many tools to call on to make a product safe, including electronic protection within the circuit itself, physical design features preventing connection of incorrect chargers, and correct allowance of space for the battery within the product envelope.
Whilst the manufacturers of high-end brands understand how to safely build and manage lithium-ion cells, many companies still risk failures in the field when they source and rebrand low-cost products from manufacturers that do not apply the necessary design practices and manufacturing controls. These products are usually designed to be as cheap as possible and, as such, often miss out many of the key safety features that the high-end brands include in their products. One example of this is the lack of thermal management. Lithium-ion cells should not be charged at temperatures above 40-50˚C, which can easily occur if the device has just been used to drive a heater (such as in cordless hairstylers or e-cigarettes) or has been left on a car dashboard (for example, portable power packs to charge mobile phones). Safe products contain internal temperature sensors to check the temperature and delay charging until the cells have cooled down. But sometimes cheap products omit this feature – risking the cells overheating, which can lead to a fire or explosion, especially if done repeatedly.
Whilst some categories of products are required to undergo regulatory safety tests, most low-voltage, battery-powered products are exempt from this, so a product with lithium-ion batteries can be launched with little or no safety testing having been carried out. Standards do exist but they may not have been implemented. Even if a product has been tested to the most common safety standards, such as UN/DOT 38.3 or IEC 62133, these standards tend to focus on the cell itself and may not offer sufficient verification that the product-level design will not cause long-term damage to the battery cells, which may lead to them failing many months after being sold. Standards do exist for usage of cells in specific product categories – but again, this relies on the product being engineered appropriately, with safety and the guidance of the standard in mind.
We would recommend that companies sourcing battery-operated products from original equipment manufacturers check proper battery design and manufacturing requirements are met and that the product has suitable back-up safety circuits to shut down the device should the primary charger or discharge circuits fail. At CDP, as well as engineering products to safely use rechargeable cells, we can also quickly analyse and test other product designs and samples to advise brand owners as to their safety and adherence with best design practices – to help avoid the risk of in-field failures and damaging product recalls. Ultimately, this is a service we would not need to offer if all products were designed and engineered with safety in mind – but we have not seen a reduction in the flow of incorrectly engineered and potentially dangerous products going to market.
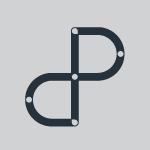
Colin Plimmer
Senior Consultant Electronics Engineer