Making it last: Why testing is vital to product sustainability
on LinkedIn:
How long do we expect a product to last? Many sophisticated technology products, such as phones and tablets, are routinely replaced after a few years as specifications evolve rapidly. But what about a chair or a toaster? There are a huge range of products that we only replace when they wear out, but how long will this take, and how do we decide when minor changes add up to justify a replacement? When we prepare new product designs, how do we test to predict whether the lifetime will be months, years, or decades?
The challenges of biomaterials
Many consumer products contain large quantities of plastics derived from crude oil. But there’s increasing consumer interest in products made from bio-based materials derived from plant matter. While bio-based plastics are renewable, many are recent innovations. There may be a temptation for designers to make a direct substitution between a well-established plastic derived from crude oil and a bio-based plastic. Yet the two materials are unlikely to behave on a “like for like” basis. Because of limited service experience, there’s often a lack of data or understanding of how new types of plastics degrade and age over time. As a result, long-term testing and lifetime predictions of bio-based materials is a particularly relevant topic and can begin right at the start of a design project, while still in the materials selection phase.
Designing for the long term
We want newly designed products to have a long service life and to withstand normal rough handling. If we buy a shiny new phone, bike, or car, we expect it to start looking slightly rough and worn after a while, but we don’t want it to break or change color too soon. How do we check for this? We need to think about how the product will be used and how it might fail.
We can look at this challenge in terms of material selection. How do products age under different applications? What types of rough handling will a product need to withstand, and will the result be sudden failure or a gradual loss of properties? How will subtle changes in the appearance of the product over time affect its suitability for continued use? Does it matter if it becomes less glossy or even changes in color? Is it easy to keep clean? Do certain design elements require local reinforcement to prevent early failures at potential weak points? It’s easy to overlook these questions when an existing product is redesigned, particularly if a change in material is proposed.
Even when changing the grade of the same plastic material, such as polypropylene, small variations in the amount or type of fillers and other additives, or the length of the polymer chains, can modify its behavior. We can’t look up a single set of properties for polypropylene as there are a huge number of grades with different characteristics. The impact of even a small change may be to move a design from rugged to marginal, with a substantially increased chance of failure. It’s vital to select specific tests in order to evaluate the risks for a particular application.
Join us to address some of the greatest environmental challenges of our era
We’re currently recruiting for a Sustainable Design Consultant, Life Cycle Assessment Engineer and a Head of Sustainability.
Better, or just different?
There are many perfectly sensible drivers for changing materials, including cost or weight reduction, improvement in properties or sustainability. In each case we seek to improve, but have we unwittingly introduced a new way in which the product might fail? If the appearance or feel of the product has changed, might it be used differently? If it appears to be stiffer and more rugged, is it OK for me to push it harder? Have we considered how to test the product design to take all possible failure modes into account? If the customer could misunderstand how to use the product there’s an increased chance of unanticipated rough handling.
If we design a product to have a long lifetime, we also need to take customer preferences into account. Until recently, there were drivers to replace products simply because they look a little old and tired. But much greater awareness of environmental issues has encouraged customers to continue to use well-liked older products until they fail, and to consider repairing them to enhance their useful life. Whatever nature can create, nature can also degrade. So, if we consider replacing a synthetic plastic with a natural material, then it may be biodegradable under the conditions of use and so it may fail in new and unexpected ways.
Mechanical performance testing is always a good place to start. As well as testing the finished product, additional trials on small pieces, or “coupons”, of the component materials will highlight any changes in properties after environmental aging. For many regulated applications, such as medical, food packaging or toys, there are specific mandatory tests, for example measuring levels of extractable or leachable materials. But in a novel design it’s often other, non-mandated tests that show up how a particular product might fail. It’s then the responsibility of the designer to investigate and mitigate the possible failure modes in a new product. Key tests will show up early signs of wear, damage or other aging and it may not be necessary to test the item to destruction.
Taking it outside
If a product is to be used outdoors or at high or low temperatures, the risk of failure must be checked over a wide range of conditions. Artificial weathering environments with water spray and UV light mean we can quickly predict the impact of many years of outdoor exposure. As well as possible changes in mechanical performance, the stability of color and other aspects of appearance can also be tested. For example, we expect the paint on a car to begin to degrade only after many years.
Specific environments will put additional stresses on some types of materials. The salt in a marine environment or the sand in a desert may cause wear much more quickly. Beneath the hood of a gas-powered vehicle, the components will be exposed to high temperatures and oil, fuel, and other fluids. Materials used in aircraft, high voltage systems and nuclear power stations also need to perform reliably in very specific ways.
Standing the test of time
Long-term subtle changes can be difficult to detect. For example, many plastics undergo creep when subjected to loads and specialized test regimes are needed to detect when substitution with a stiffer material is necessary. Exposure to fluids can also cause long-term changes, particularly when plastics slowly absorb the fluid and become softened and distorted.
If a product is designed to last for decades, for example if it’s installed within a building, then we need to carry out accelerated aging evaluation to test how its properties will perform over this period. One response is to apply the rule that the rates of chemical changes increase with temperature in a predictable, mathematical way.
By storing samples in ovens at a range of elevated temperatures and testing them periodically, we can build a picture of how the same material will perform over decades at room temperature. This methodology is often termed the Arrhenius approach. For example, it may allow us to predict behavior after 10 years at 20°C in only around six months, by accelerating the testing at 60°C. We can even immerse the accelerated test samples in fluids if we want to simulate use in wet conditions, for example in food or beverage applications.
A route through the maze
With appropriate experience in design, material selection and evaluation, it’s possible to devise a new product and to put together a suitable test plan. The data generated can be applied to provide confidence that a new design or a change of material will lead to a product with a long lifetime. After all, when we like a pair of shoes, we want them to wear out slowly, and there’s no reason why the same can’t apply to our favorite products.
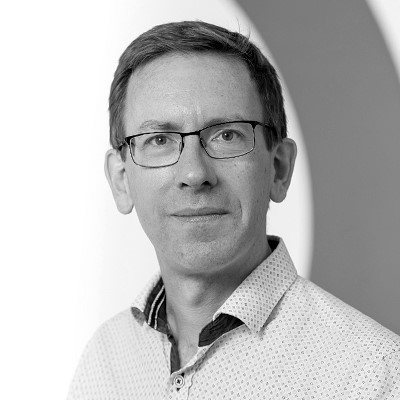
Jonathan Wilkins
Senior Consultant Mechanical Engineer
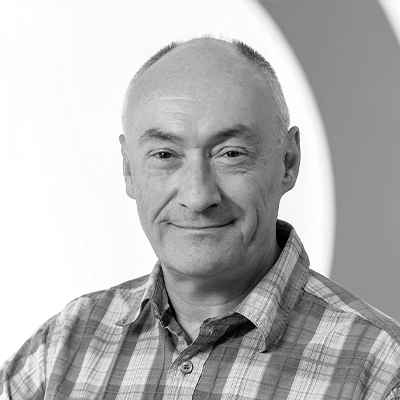
Mark Buckingham
Senior Consultant Chemist