Looking inside innovation
on LinkedIn:
Anybody who has ever tried to make anything knows that sinking feeling when you put your invention together for the first time, press go and… nothing happens. Or, worse, a lot happens that you really weren’t expecting! Assuming your prize creation hasn’t actually exploded (SpaceX, we’re looking at you), you’re probably wishing you could see inside to find out what’s wrong. Well, you can, and it’s easier and cheaper than you might think – thanks to computerised tomography (CT) scanning.
CT scanning is nothing new – most of us are familiar with the large ring-shaped machines you lie inside in hospital to be diagnosed – but it has also been used in industry since it was invented in the early 1970s. But, as with most other imaging techniques, the resolution, accuracy and speed of CT scanning has increased exponentially in the last four decades.
Industrial CT scanning works in exactly the same way as hospital scanning – an object is X-ray imaged from many different angles, then the images are reconstructed (that’s the ‘tomography’ bit) into a 3D computer model that shows all the external and internal features at the same time. This can then be interrogated on your PC to take sections, measure features in 2D and 3D, and perform any other feat of image processing you care to imagine. What you actually see in these scans are changes in X-ray attenuation – usually this equates to a change in material type or material density. So you can see (and measure) the shape of things but also any cracks, voids, contamination or anything else that affects how well a material absorbs X-rays.
This list will immediately get any manufacturing quality engineer salivating. And CT scanning is a popular tool in manufacturing environments – even supporting the manufacturing processes themselves. It’s great for this because the measurement process is non-contact, very repeatable and can measure features not possible with conventional contact or optical systems. The flexibility of CT scanning means that it’s applicable to a very wide range of parts and, if the part specification changes, the measurement process can be updated rapidly.
For designers, though, verification and validation against a pre-determined specification is only part of the appeal of CT scanning. When you get a CT scan, you get a treasure trove of data – literally gigabytes of it. It’s possible to compare the part with the original computer-aided design model, or another part, to see a comparison ‘heat map’ of errors that can offer much more information than any individual measurements. Are two parts in an assembly clashing because they were made wrong or because one is deforming under load in unexpected ways? How does a pressure vessel change dimensions between empty and pressurised? Does cycling the design through its life lead to cracking that could cause failures? When you don’t know what you don’t know, rich data like that produced from a CT scan can provide valuable – and sometimes unexpected – insights.
Another key advantage over other imaging or measurement techniques is the ability to see inside assemblies, particularly when opening them up to look inside isn’t possible or destroys the evidence you are trying to collect. This ability to see inside working products at different time points has, for example, revolutionised battery research, where suddenly scientists could watch lithium ion cells deteriorate with charge/discharge cycles, study the underlying processes and ultimately figure out solutions. This high-quality, non-destructive testing, made possible by CT scanning, is partly responsible for developments in battery technology that most of us benefit from every day.
The potential impact on innovation can be similarly substantial. The ability to measure almost any feature allows for the design, testing and validation of more complex parts, which leads to cheaper and higher performing products. When these parts are put together, the ability to rapidly learn about the performance of the assembled product in a non-destructive way shortens development cycles and allows products to be launched faster and with lower risk. And that’s good news, whichever way you look at it…
Image courtesy of ZEISS
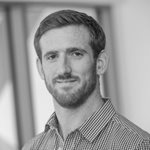
Matt Morris
Senior consultant mechanical engineer