Product design: Is plastic ever the best choice?
on LinkedIn:
Plastics’ reputation has gone from miraculous to maligned in the last half-century. Suppliers have even resorted to disguising their use with brand names and faux-natural finishes. However, if good product design means selecting the right tool for the job, there are many applications where these unfashionable materials may still be the best choice in products with design lifetimes of many years.
Below we look at the case for considering plastics in the design of durable products, and why they don’t need to spell disaster for the environment when used responsibly.
The rise and fall of plastics
Short for ‘thermoplastic’, the term ‘plastics’ describes materials that will soften and melt under heat, meaning they can be molded into intricate shapes at moderate cost.
The first synthetic plastic was patented in 1907, and by the mid-20th century, plastics were enjoying a heyday. As manufacturing techniques and costs improved, products, such as plastic bags and cling film wrap, became prolific. By the end of the century, the realization that these packaging materials could take thousands of years to break down (and may cause environmental harm when they do so), resulted in an anti-plastic movement.
The challenge for today’s innovators is that the case for durable-use plastics got swept up in the backlash against single-use items. There have also been many examples of low-cost reusable plastic items which are often thrown away after being used for only a brief time. This has made it harder to convince manufacturers, product designers, and consumers that sometimes plastics may be the most suitable option for products designed to be used for ten years or longer.
When plastic may be the only choice
There are many factors to consider when choosing the most appropriate material for an application: properties, price, ease of processing, and sustainability. These have different weightings depending on the intended application.
For example, in ‘life-or-death’ products, a material’s properties will often outweigh its eco-score. For example, would you choose a biodegradable yet less effective version of the following: a bulletproof vest, hospital machinery part, or heart valve? In less critical applications, choosing between different materials may be more finely balanced, and selecting a material that permits a long design-life remains a key factor.
Join us to address some of the greatest environmental challenges of our era
We’re currently recruiting for a Sustainable Design Consultant, Life Cycle Assessment Engineer and a Head of Sustainability.
A versatile material
Plastics’ original (and ongoing) attraction is that they can be blended with additives, such as colored pigments, stabilizers, antioxidants, flame retardants, and reinforcing fillers, to take on an incredible range of properties. The flip side of these additives is that they make recycling harder, so they should only be included when they provide an important benefit. The range of properties includes:
- Durability – plastics’ perceived environmental weakness can also be its strength: if a plastic product works well and is designed to last many years, it’s a better solution than an alternative with a shorter lifetime. Buried PVC plastic pipes outlast iron or concrete pipes, with a service life of over 100 years.
- Resistance to bacteria – more relevant than ever is the ability of specially-designed additives to make some plastics repel or inhibit the growth of microorganisms. As well as reducing the transmission of disease, the product’s lifetime may also be extended.
- Heat and electrical resistance – most electrical products need housing to keep dust, water, and fingers away from live current. It must be electrically insulating, protect components, and provide an opportunity for branding and ergonomics. For many applications, plastic housing is more suitable than metal.
- Density – the low comparative weight of some plastics can lead to them becoming the most sustainable option. For example, replacing metal parts with plastics in cars makes a vehicle lighter. A 10% drop in weight leads to a 6-8% improvement in fuel economy. That’s a lot of fuel (or electricity) over its lifetime.
- Ease of manufacture – the processing temperatures of plastics are much lower than for glass or metal, and less energy is needed to heat the material for manufacture. Substituting plastics with alternatives would increase lifecycle energy consumption by over 50%.
- Availability – the materials which form plastics can be any one of a wide range of synthetic or naturally derived polymers. As issues around sourcing and disposal become increasingly important, this is leading to the increasing selection of bioplastics in some applications.
‘Designing in’ the responsible use of plastics
A comprehensive design process should look at the whole lifecycle of any material, including sourcing and afterlife. Here are three ways to ensure plastic is used responsibly:
Look for sustainable sources. In the medium to long term, all plastics will need to come from a renewable resource. In many cases, a part- or wholly recycled material may be suitable. Lego, for example, has started designing its bricks from recycled plastic bottles. Designing with plastics, such as nylon and polyethylene, for which plant-based sources are already available, enables these to increasingly compete with fossil-fuel sources.
Design for ease of repair and longevity. In our article, Making it last, we looked at how materials and design can work together to ensure a long useful product lifetime. The ‘Right to Repair’ will become increasingly important for durable products. Where wear is anticipated, the product should be designed so individual parts can easily be repaired or replaced. We examined these issues in the context of electronic products in another article, Ten ways to reduce e-waste in product development. Many of the same principles may be applied to reduce plastic waste.
Take responsibility for the afterlife of plastics. We can design plastic products with as long a lifetime as possible. Still, we also need to consider their eventual disposal and the likely changes in regulations during the product lifetime. The diversity of plastics means it’s hard to recycle them all. Manufacturers will need to take increasing responsibility for the fate of products at the end of their useful life. They will also be required to work locally with legislators to design waste streams so plastic products are specifically designed for ease of recycling and users are incentivized to recycle or reuse them whenever possible.
The right material for the job
Evaluating materials is a key element of product design. Putting a product’s intended application at the center of this choice leads not only to a better end-user experience but can be the more sustainable option too.
References
- PVC Pipe Longevity Report [Internet]. UTAH State University. 2014 [cited 18 January 2022]. Available from: https://www.ipexna.com/media/3074/pvc-pipe-longevity-report.pdf
- Water Storage Tanks with Antimicrobial Technology [Internet]. Ultra-Fresh. 2019 [cited 18 January 2022]. Available from: https://www.ultra-fresh.com/water-storage-tanks-with-antimicrobial-technology
- Selecting the Right Materials for Industrial Enclosures [Internet]. Machine Design. 2019 [cited 18 January 2022]. Available from: https://www.machinedesign.com/materials/article/21837832/selecting-the-right-materials-for-industrial-enclosures
- A Vision on the Future of Automotive Lightweighting [Internet]. Lightweight-alliance.eu. 2019 [cited 18 January 2022]. Available from: http://lightweight-alliance.eu/wp-content/uploads/2019/11/alliance_vision-document.pdf
- Plastics and Oil Consumption [Internet]. BPF. 2019 [cited 18 January 2022]. Available from: https://www.bpf.co.uk/press/oil_consumption.aspx
- Sustainable Manufacturing: What bioplastics means for your business [Internet]. Essentra Components. 2021 [cited 18 January 2022]. Available from: https://www.essentracomponents.com/en-gb/news/news-articles/sustainable-manufacturing-what-bioplastics-means-for-your-business
- Lego plans to sell bricks from recycled bottles in two years [Internet]. BBC News. 2021 [cited 18 January 2022]. Available from: https://www.bbc.co.uk/news/business-57575991
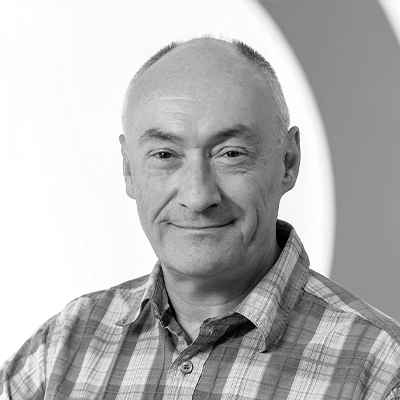
Mark Buckingham
Senior Consultant Chemist
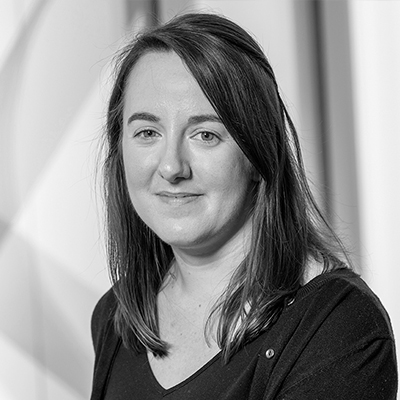
Amy King
Innovation Consultant